橡胶疲劳性能研究进展
刘宇艳 万志敏
摘要:综述了动态载荷下疲劳对橡胶物理机械性能的影响、影响橡胶疲劳的因素、橡胶疲劳性能的研究方法及橡胶疲劳的机理。指出橡胶制品的疲劳寿命取决于橡胶的抗疲劳断裂性能,研究橡胶的疲劳特性对于结构抗疲劳设计和疲劳寿命预报模型的建立是极其重要的。
关键词:橡胶;疲劳;裂纹;疲劳机理;综述
中图分类号:TQ330.7 文献标识码:A
文章编号:1000-1255(2000)02-0128-04
Progress on fatigue properties of rubber
Liu Yuyan and Wan Zhimin
(Department of Applied Chemistry,Harbin Institute of Technology)
Abstract:The factors influencing rubber fatigue,the effect of fatigue
on rubber physical properties and research approaches of rubber fatigue and fatigue damage
mechanisms under dynamic load were reviewed with 24 references.It was pointed out that the
fatigue life of rubber products depended on the fatigue fracture resistance of rubber
materials and the research of rubber fatigue was very important for the structure fatigue
resistant design and the estalishment of fatigue life prediction model.
Keywords:rubber;fatigue;crack;fatigue mechanism;review
橡胶制品通常是在周期性应力状态下使用的,橡胶材料的疲劳断裂性能往往决定这些制品的疲劳寿命。为了保证橡胶制品使用时的安全性和可靠性,研究橡胶材料的动态疲劳特性具有重要的意义。
1 疲劳对橡胶物理机械性能的影响
对炭黑填充的天然橡胶(NR)硫化胶在一定负荷下多次拉伸变形时物理机械性能的研究结果表明[1],橡胶的物理机械性能在疲劳的初期和末期呈现不同的变化趋势。在疲劳过程中,拉伸强度先是上升,经过极大值后趋于下降,而撕裂强度、动态弹性模量和力学损耗系数的变化则相反。由初始值和极大(小)值的比较可知,拉伸强度增大约20%,撕裂强度减小约80%,动态弹性模量减小约60%,力学损耗系数减小约10%。轮胎胎面胶在实际使用中发生的物理机械性能的变化也具有类似的倾向[2]。
Beatty研究了在氮气中拉伸周期对NR物理机械性能的影响,结果表明[3],在疲劳过程中,拉伸强度几乎保持不变;300%定伸应力在疲劳初期明显增加,然后增加趋缓;扯断伸长率随疲劳周期的变化而下降。改变空气氛围(如氧和臭氧等)和应变周期可以得到相同的结果。填充炭黑的丁苯橡胶(SBR)、氯丁橡胶(CR)、丁基橡胶(IIR)和丁腈橡胶(NBR)的扯断伸长率随疲劳周期的变化趋势相同。
2 影响疲劳寿命的因素
弹性体性质影响疲劳寿命最重要的因素是弹性体的性质。研究表明[1],在低应变疲劳条件下,橡胶的玻璃化转变温度愈高,耐疲劳破坏性能愈好;在高应变疲劳条件下,具有拉伸结晶性的橡胶耐疲劳破坏性能较好。疲劳裂纹增长也与弹性体种类有关,NR和BR对应变速率不敏感,而SBR等由于具有较大的粘弹性,对应变速率较为敏感[4]。
应变周期对NR胶料的研究结果表明[3],最小应变增加时尽管能量输入降低,但样品的疲劳寿命却增加,说明施加于样品的最小应变是影响疲劳寿命的主要因素。还有许多橡胶制品的例子表明应变周期在很大程度上影响制品的性能。
操作温度操作温度对橡胶耐疲劳破坏性能的影响相当复杂,因为疲劳中同时发生了不可逆的化学变化(如降解)。另外高温还影响材料的模量和扯断伸长率。但在大多数试验中,随温度的增加,NR和SBR的疲劳寿命都降低,只是前者不如后者明显[5]。
空气氛围空气氛围对橡胶疲劳裂纹增长的影响也比较显著。一般惰性环境(如氮气)使疲劳裂纹增长速率下降,氧和臭氧使疲劳裂纹增长加速。与氧的影响相比,臭氧裂纹可在更低的应力下发生,0.5×10-6的臭氧可以使疲劳裂纹增长速率增加40%~80%[4,5]。
此外,填料、硫化系统、硫化状态、抗氧剂对橡胶的疲劳性能均有一定的影响。
3 橡胶疲劳性能的研究方法
3.1 以断裂力学为基础
3.1.1断裂力学理论
Rivlin等[6]曾将断裂力学应用于橡胶疲劳性能的研究,提出将以弹性能为基础的参数用于研究橡胶疲劳性能。能量法使不同几何形状和变形样品的裂纹增长结果发生联系,裂纹增长和疲劳寿命定量地联系起来奠定了将实验测试和使用情况相关联的基础。Rivlin等将裂纹每增长单位面积所释放的能量称为撕裂能(T),其数学定义式为
(1)
式中,U为贮存在样品中的弹性应变能,A为裂纹的一个断裂表面的面积(未应变状态)。
实验表明[5,7~9],裂纹增长速率与撕裂能之间的关系与样品的几何尺寸无关。在周期载荷下,样品的裂纹增长速率为
(2)
式中,c为裂纹长度,n为疲劳周期数。裂纹从c1增长到c2所需的疲劳周期数可以通过积分式(2)得到
(3)
代入T与c的关系式,就可定量地得到疲劳寿命与橡胶的裂纹增长特性、变形幅值、初始裂纹或缺陷尺寸的关系。
3.1.2典型结果
NR和SBR硫化胶的疲劳裂纹增长数据与撕裂能的关系表明[8,9],疲劳裂纹增长特性曲线主要包括4个区域:撕裂能很小时,裂纹增长速率与撕裂能无关;撕裂能高于临界撕裂能(T0)时,有如下关系式:
(4)
当撕裂能高于Ta时,存在如下关系式:
(5)
式中,B和m均为材料常数,其值与材料结构、频率、温度和环境有关;当撕裂能达到失效撕裂能时,dc/dn为无穷大,断裂发生。
3.1.3试验结果与使用性能的关系
斜胶胎的花纹沟裂纹有人曾应用裂纹张开技术估算撕裂能,分析了卡车斜胶胎的花纹沟裂纹增长速度。采用纯剪切试样模拟中心花纹沟基部的应变,实验结果(假设最大花纹沟应变为9%)与卡车在实际路面上一圈的裂纹增长结果比较一致[8]。Lake用纯剪切件模拟研究了斜胶胎的胎面花纹沟和子午线轮胎胎侧的动态应变,探讨了它们对裂纹增长特性的影响。实验表明,花纹沟裂纹和胎侧裂纹都受胶料切口增长参数和撕裂能的控制[9]。
子午线轮胎的胎侧裂纹Young[10]采用带有预切口的拉伸试样得到了NR/BR共混物的疲劳裂纹增长数据,将该结果与胎侧裂纹增长结果相比较,当胎侧应变为21%时,两者有较好的一致性。Young认为采用液压系统测试纯剪切试样可以得到高质量的应变能相对密度和疲劳裂纹增长(FCG)数据[11]。纯剪切试样的厚度不小于2mm时,可以测出大部分材料的FCG值;应变为15%时,实验值与轮胎转鼓试验的胎侧裂纹增长数据具有很好的一致性。
轮胎油皮胶和带束层隔离胶的裂纹Young以断裂力学为基础,采用FCG数据对炭黑在CR/NR共混物中的分布、轮胎油皮胶用溴化丁基橡胶及带束层隔离胶进行了评价。结果表明,FCG法可以对轮胎胶料进行研究与筛选[12]。
3.2 以疲劳寿命曲线(S-N)为基础
S-N曲线在金属材料中已得到广泛应用,但在橡胶材料中应用较少,因为对橡胶制品而言,疲劳寿命一般高达106~108次,为得到一点的数据需要相当长的时间。因此,深崛美英等[13]提出了Demattia等加速试验方法,能简单地求得从高应变至低应变的S-N曲线。首先求得具有不同预加伤痕(C)的一连串试样的λ-lgN(λ为拉伸比,N为疲劳寿命)曲线,然后使这些曲线沿着疲劳寿命轴平行移动,且与未试试样的S-N曲线(C等于C0,C0为未试试样潜在缺陷的尺寸)重叠,从而获得标准曲线。应用断裂力学和前人的研究成果,作者得出了λ-lgN的理论关系式:

式中,G和β为有关裂纹增长的材料常数,E为弹性模量。
比较未增强天然橡胶和炭黑增强天然橡胶(图1)的合成S-N曲线与理论S-N曲线可以看出,2条曲线大体上是一致的,只是合成S-N曲线在低应变区域比理论S-N曲线更具有向下偏移的倾向。
傅政等[14,15]用深崛美英提出的方法研究了NR/BR的动态疲劳与断裂特征,为最佳共混比的选择提供了理论依据。NR/BR共混物的β随BR用量的增加而增大,意味着裂纹的扩展速度增加,而C0却明显减少,同时表征了用Demattia等加速试验法得到的合成S-N曲线的变化规律。他们综合分析后认为,NR/BR(质量比)为60/40~70/30时,共混物的动态疲劳破坏性能较好。裘怿明等[16]用多项式回归方法拟合了NR/BR共混物的疲劳断裂曲线,结果表明实验值与理论值吻合良好。
右田哲彦[1]曾以S-N曲线为基础,研究多应力条件下的疲劳累积加和法则(Miner法则)对硫化橡胶是否适用,发现在轻缓条件(重复应力为拉伸强度的20%)加苛刻条件(重复应力为拉伸强度的90%)时,Miner法则成立;在苛刻条件加轻缓条件时,Miner法则不成立。
疲劳试验数据的离散性、构件加工尺寸的偏差、橡胶中分布的原始缺陷以及受载时危险部位应力响应的分布特性等都说明应力和强度,以及影响它们的因素都是随机变量,具有各自的分布形式。只有运用概率统计理论和方法来处理才能正确预测橡胶的疲劳特性和可靠寿命。另外,Miner法则已不适用于橡胶材料,需对其进行改进,提出新的疲劳累积法则。
4 橡胶材料的疲劳破坏机理
已经有一些研究者应用扫描电子显微镜(SEM)技术对橡胶材料的疲劳破坏机理进行了研究[17~19]。Mathew的研究表明[20],未增强橡胶表现为塑性破坏,而炭黑填充的橡胶则表现为脆性破坏,且随着防老剂的加入,其破坏态向准塑性转变。傅政等[14]采用SEM研究了NR/BR共混物的疲劳断裂特征,发现若NR/BR的共混比不同,共混物的断面形貌也具有明显的差异。刘卫东等[21]则用SEM对NR/BR共混物的拉伸疲劳破坏断面进行了研究,发现试样拉伸疲劳破坏断面具有拉伸断裂和屈挠龟裂双重特征。
刘约翰和张士齐等[22,23]采用电性能和声性能等宏观手段测定了硫化胶疲劳前后性能的变化。研究表明,填充炭黑硫化胶的体积电阻率在疲劳后有所增加。但由于炭黑粒径及结构等的影响,炭黑在硫化胶内含量不同时,疲劳后硫化胶体积电阻率的变化也不同。对NR疲劳前后声速变化的研究表明,疲劳后声速下降。硫化胶的配方不同,声速下降率也不同。张士齐等[24]还用红外光谱对NR疲劳前后的化学结构进行了分析,发现在疲劳初期(2×104次),NR在产生键断裂的同时产生交联和直链键合。继续疲劳至10×104次时,单硫直链键的浓度大幅度下降,链断裂占优势,试样出现宏观的1级裂口。
5 小结
橡胶的疲劳破坏已引起人们的重视,但以往主要是研究橡胶材料的宏观疲劳性能、裂纹增长特性和疲劳破坏特征,并没有从疲劳的本质出发对疲劳现象进行恰如其分的描述。深入研究橡胶材料在疲劳过程中的破坏机理及其与宏观性能的关系,对于其结构抗疲劳设计及疲劳寿命预报模型的建立都是极其重要的。
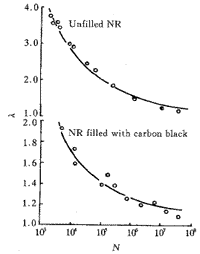
Fig1 Comparison of compositionS-Ncurvewith
theoreticalS-Ncurve
○Experiment,-alculated curve
基金项目:哈尔滨工业大学基金资助项目(1822)。
作者简介:刘宇艳,女,28岁,讲师。已发表论文17篇。
刘宇艳(哈尔滨工业大学应用化学系,150001)
万志敏(哈尔滨工业大学应用化学系,150001)
参考文献
[1]右田哲彦.橡胶的疲劳与破坏关于机理与配方设计[J].橡胶译丛,1981,2:1~19
[2]村上伸兹.大型轮胎行驶后胎面胶的疲劳情况[J].轮胎工业,1989,8:25
[3]Beatty J R.Fatigue of rubber[J].Rubber Chemistry and Technology,1964,37:1 341
[4]Young D G. Fatigue crack propagation in elastomer
[5]compounds:Effects of strain rate,temperature,strain level and oxidation [J].Rubber
Chemistry and Technology,1986,59(5):809~ 825
[6]Lake G J.Mechanical fatigue of rubber[J].Rubber Chemistry and
Technology,1972,45(1):307~ 328
[7]Rivlin R S,Thomas A G.Rupture of rubber.Ⅰ .Characteristic energy for tearing[J].J
Poly Sci,1953,10(3):291~ 313
[8]Kim S G,Lee S H.Effect of crosslink structure on the fatigue crack growth behavior
of NR vulcanizates with various aging conditions[J].Rubber Chemistry and
Technology,1994,67(4):649~ 661
[9]Young D G.Application of fatigue methods based on fracture mechanics for tire
compound development[J].Rubber Chemistry and Technology,1990,63(4):567~ 581
[10]Lake G J.Fatigue and fracture of elastomers[J].Rubber Chemistry and
Technology,1995,68(2):435~ 460
[11]Young D G.An innovative approach to fatigue cracking in elastomers[J].Rubber
Chemistry and Technology,1982,55(23):428
[12]Young D G,Fatigue and fracture of elastomeric materials[J].Rubber World,1991,3:30~
34
[13]Young D G.Dynamic property and fatigue crack propagation research on tire sidewall
and model compounds[J].Rubber Chemistry and Technology,1985,58(4):785~ 805
深崛美英.弹性体疲劳寿命的预测[J].橡胶译丛,1986,4:67~76
[14]傅政,谷恒勤,朱东兵等.天然橡胶/顺丁橡胶共混物的动态疲劳与断裂特征[J].橡胶工业,1992,39(2):107
[15]傅政,谷恒勤,朱东兵等.BR胶料的疲劳断裂特征[J].合成橡胶工业,1992,15(4):235
[16]裘怿明,傅政,刘旭阳等.多项式回归拟合NR/BR共混胶料疲劳断裂曲线[J].橡胶工业,1998,45:137
[17]Hirakawa H,Urano F,Kida M.Analysis of fatigue process of rubber
vulcanizates[J].Rubber Chemistry and Technology,1978,51(2):201
[18]Omura N,Takahashi M,Nakamura T.The fatigue properties of silicone
rubber[A].Presented at the Meeting of the Rubber Division[J].Washington Hilton:American
Chemical Society,1990
[19]罗滕丽,霍玉云.丁基再生胶与高不饱和度二烯橡胶并用体系耐疲劳性能研究[J].橡胶工业,1991,38(9):516
[20]Mathew N M,Bhowmick A K,De S K.Chemical and scanning electron microscopy studies
on fatigue failure of natural rubber vulcanizates[J].Rubber Chemistry and
Technology,1982,55(1):51~ 61
[21]刘卫东,顾建明,金政吉等.天然橡胶/顺丁橡胶并用硫化胶的力学破坏机理[J].橡胶工业,1994,41(5):260
[22]刘约翰,展圣仙,叶林忠等.天然橡胶硫化胶疲劳后电性能的变化[J].橡胶工业,1989,36(8):452
[23]张士齐,刘约翰,黄静贤等.用声速研究硫化橡胶的疲劳性能[J].橡胶工业,1990,37(7):416
[24]张士齐,周翠薇,邓知庆等.研究炭黑补强硫化橡胶疲劳的分子历程[J].橡胶工业,1988,35(10):616
收稿日期:1999-01-14;修订日期:1999-12-20。 |